クリーンディーゼルエンジン
黒煙が出るとかで、なにかと目の敵にされがちなディーゼルエンジンだが、車の排ガス対策の歴史をひもとくと、ガソリンエンジン用の排ガス浄化用触媒(三元触媒)が出現するまでは、ディーゼルエンジンは低公害エンジンだったのだ。三元触媒が出現しても、直噴のガソリンエンジンが実用化されてもなお、CO2排出量ではディーゼルにかなわない。そのため環境問題に熱心なヨーロッパでは、乗用車でもディーゼルエンジンのシェアが非常に高く、50%弱となっている。
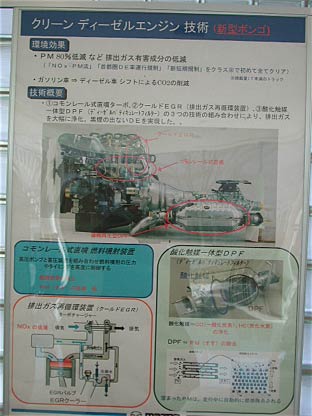
ディーゼルエンジンのクリーン化技術には、エンジン自体の工夫(コモンレールなど)と触媒等の後処理システムの2つに大別される。今回紹介するのは後処理技術の方だ。下の写真は、酸化触媒(HCとCOを浄化する)とDPF(黒煙を取り除く)が1つの金属ケースの中に入っている。酸化触媒は三元触媒とほぼ同じ原理で作動する。つまり排ガスの温度でHCとCOを排ガス中に含まれる空気と反応させて燃焼させ、CO2にして浄化するのだ。
一方DPFはかなり変わっており、中がフィルターとなっている。そこに黒煙だけをトラップし、溜まった黒煙を後で燃やすのだ。
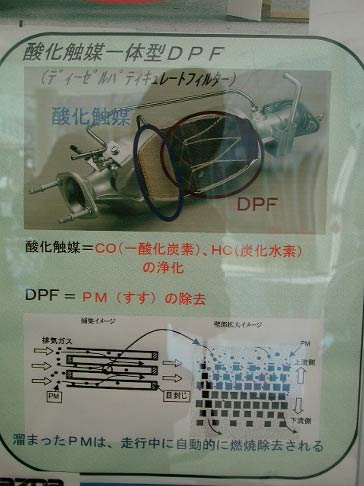
左の肌色をしているのが酸化触媒、黒いのがDPFだ。DPFは何か変な模様をしている・・・
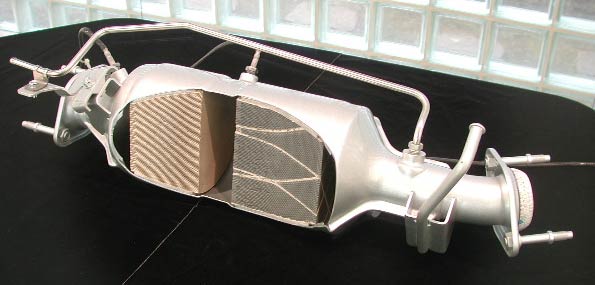
反対側から見たところ。DPFの方は、何か白い筋が入っているが、実はこれがミソ。DPFの考え方自体は大昔からあり、酸化触媒に使われている肌色と同じ材料(コージェライト)が使われていた。しかしこれは熱に弱く、トラップした黒煙を燃やすとき溶けてしまい、排ガスが流れなくなるトラブルが発生し、本格的な実用の域に達しなかった。
一方黒いDPFの材質は炭化珪素(SiC)。コージェライトに比べて熱に強いため黒煙を燃やしても溶ける可能性は少ないことは昔から知られていたのだが、熱衝撃(急激な温度差)に弱く膨張差で割れが発生するため、これまた実用化されなかった。ところがSiCを直方体の小さなユニットに分割したものを、白い筋の接着剤でひっつけたところ、接着剤が緩衝剤となり割れの問題が解決してしまったのだ。驚くべき事に、この画期的技術を実用化したのは、自動車とは今まであまり縁のなかったイビデンという電気材料のメーカーである。
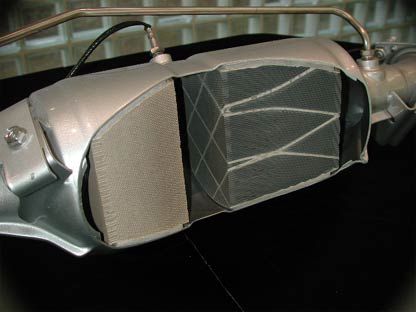
こうした技術でディーゼル排ガスはクリーンになるのだ。